4.2 miliardi di tonnellate di materiale prodotte per 2.2 miliardi di tonnellate di CO2 emesse ogni anno. Per limitare il global warming la transizione energetica deve investire anche la filiera del cemento, un settore dall’enorme impronta ecologica. Ma che offre già oggi soluzioni sostenibili e poco inquinanti
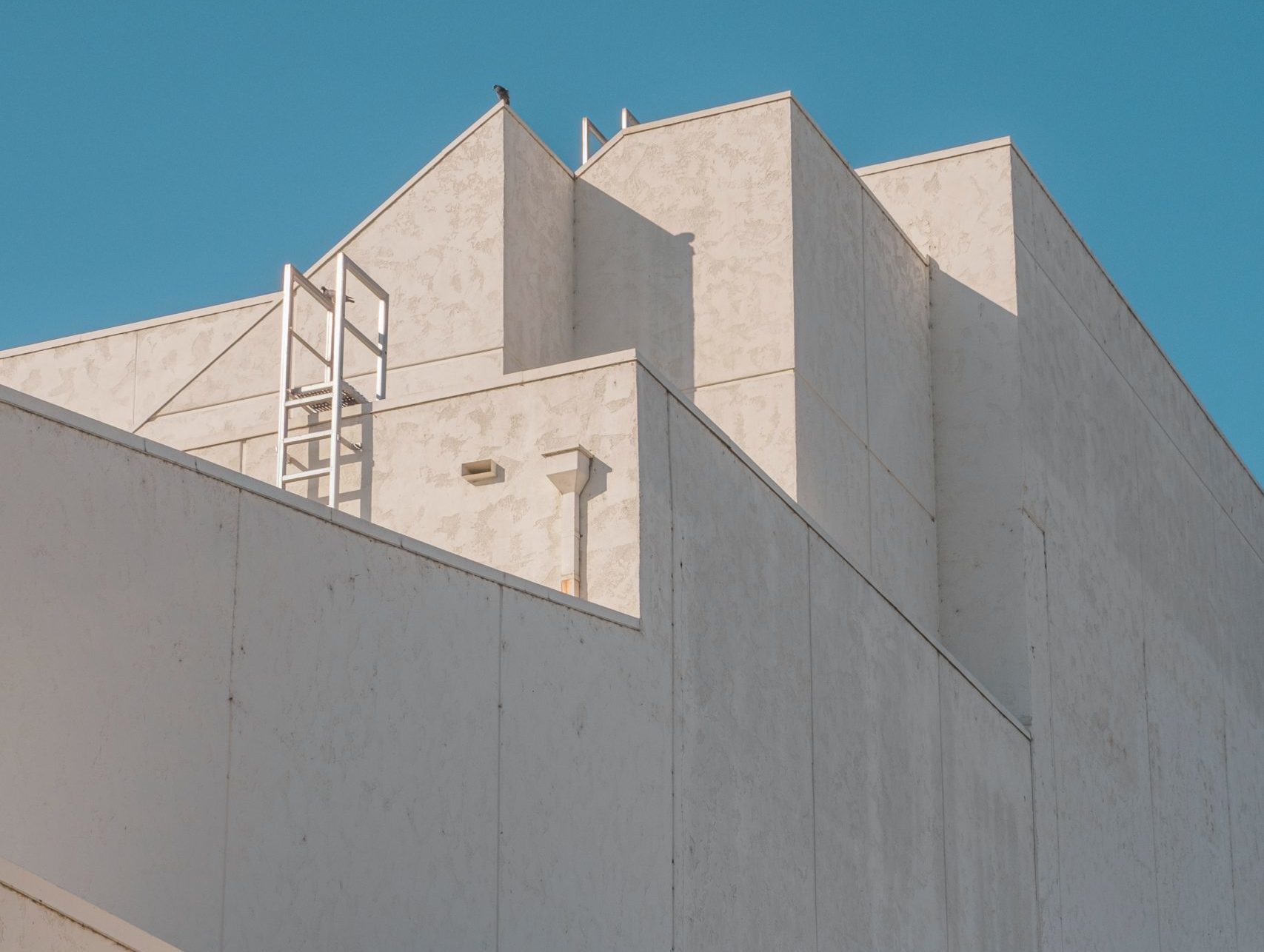
di Matteo Grittani
(Rinnovabili.it) – È il materiale prodotto dalle mani dell’uomo più diffuso sul pianeta e genera un volume d’affari di un miliardo di miliardi ogni anno compreso l’indotto. I primi esempi di suoi “lontani antenati” risalgono addirittura a 1300/1400 anni prima di Cristo. A quel tempo infatti, i costruttori tra le attuali Siria e Iraq cominciarono a coprire le loro abitazioni di argilla pressata con un sottile strato di gesso e calcare che, una volta scaldati, reagivano con l’aria circostante per formare un aggregato robusto che proteggeva la superficie: era nato il cemento.
Con questo termine oggi si indica il legante che tiene insieme inerti come sabbia, ghiaia e pietrisco che vanno poi a costituire il calcestruzzo oppure, qualora uniti ad un’armatura di tondini d’acciaio, il cemento armato. A distanza di centinaia di anni dalla scoperta, il cemento e i suoi derivati sono diventati piatto forte degli skyline cittadini contribuendo tuttavia in maniera sensibile all’inquinamento e alla generazione di anidride carbonica.
I numeri del cemento nel mondo
Se il cemento fosse un Paese, sarebbe il terzo emettitore globale subito dietro a Cina e Stati Uniti: conta circa l’8% della CO2 globale prodotta dall’uomo ogni anno. Secondo il think-thank londinese Chatham House che ha i dati più aggiornati, sono più di 4 i miliardi di tonnellate di materiale grezzo prodotte ogni anno. Una cifra destinata a lievitare di un ulteriore miliardo entro il 2030, spinta dalla crescente urbanizzazione e dallo sfruttamento del suolo incontrollato specie nel Sud e Sud-est asiatico.
Ma in che modo la produzione stessa del cemento genera questa enorme quantità di anidride carbonica? I combustibili fossili sono fondamentali per permettere la reazione chimica preliminare che crea il cemento – quella che trasforma il calcare in clinker – e servono per sostenere i processi successivi tramite enormi quantità di calore nei cosiddetti kiln (gli altoforni). Considerando anche i metodi meno energivori disponibili oggi per produrlo, ogni tonnellata di cemento messa sul mercato genera dai 510 ai 712 kg di anidride carbonica secondo la letteratura scientifica più aggiornata. È davvero troppo. Nonostante una certa refrattarietà del settore edilizio e delle costruzioni al cambiamento, in un’ottica futura di transizione energetica è auspicabile che l’inefficienza dei processi produttivi e l’inquinamento associato lascino spazio ad una crescente attenzione alla sostenibilità energetica e ambientale di tutto il ciclo vita di questo materiale così importante per l’uomo.
Alla fine del 2019 la Global Cement and Concrete Association (GCCA), che rappresenta il 30% del mercato cementizio globale, ha presentato le sue linee guida “per una filiera del cemento sostenibile” che comprendono degli emission cap, ovvero dei tetti alle emissioni per quantità di materiale generato che interessano particolato, ossidi di azoto, zolfo e composti volatili organici, così come limiti sull’utilizzo di acqua ed energia per ogni fase del processo. Certo, non sarà cosa facile allinearsi agli obiettivi contenuti nelle “Sustainability Guidelines” di GCCA, soprattutto per gli ingranaggi di un meccanismo costruttivo vecchio di centinaia di anni. Per fortuna l’avanzamento tecnologico e la ricerca stanno dando i loro frutti: ad oggi esistono centinaia di progetti e concept – alcuni già sul mercato – che rivoluzionano la filiera del cemento con l’obiettivo di ridurre drasticamente le emissioni e gli inquinanti che crea.
I progetti principali
Il primo degno di nota parte da un’idea dalla Rutgers University ed è stato messo a punto dalla start-up statunitense Solidia. L’azienda è in grado di tagliare del 70% la quantità di CO2 emessa durante la lavorazione; gli ingegneri della Rutgers hanno creato infatti una nuova “ricetta” per produrre cemento sostenibile che fa più uso di argilla e meno di calcare. Le temperature per far avvenire le reazioni non superano mai i 240 gradi Celsius e il materiale derivato ha prestazioni simili al cemento convenzionale “Portland” sia in termini di durabilità, che di resistenza a compressione e deformazione. Come se non bastasse è più economico, oltre che notevolmente meno energivoro.
Un altro metodo interessante che questa volta arriva dal Canada e che ha già permesso di salvare 100 mila tonnellate di CO2 in pochi anni di produzione è quello di CarbonCure. La loro tecnologia sfrutta la mineralizzazione della CO2 secondo cui un getto di anidride carbonica viene iniettato nella miscela di cemento in lavorazione per poi reagire con gli ioni Calcio contenuti nel conglomerato e formare un minerale dalle dimensioni nanometriche: il carbonato di calcio (CaCO3). Quest’ultimo viene inglobato nel cemento solido con la conseguenza da un lato di migliorare le sue caratteristiche prestazionali e dall’altro di eliminare CO2 proveniente da altri processi industriali invece di crearne di nuova come sottoprodotto. Sembra fantascienza, eppure è già realtà: l’azienda di Dartmouth ha già prodotto e consegnato ai clienti quasi un milione di carichi di cemento con questo metodo di produzione in poco più di 5 anni.
Poco distante, a Montreal, c’è CarbiCrete che sfrutta un meccanismo simile – ovvero inietta CO2 nella miscela che costituirà poi il calcestruzzo. A differenza dei metodi precedenti tuttavia, questo si sbarazza completamente del cemento come legante, che viene sostituito invece da un sottoprodotto della lavorazione dell’acciaio chiamato steel slag. Gli slag sono vere e proprie scorie da fonderia simili al vetro, i cui costituenti principali sono ossidi di metallo e biossidi di silicio. Con il procedimento usato da CarbiCrete si risparmiano 2kg di CO2 per ogni blocco di calcestruzzo prodotto mentre un ulteriore kg viene iniettato e “sequestrato” nel materiale stesso; per questo l’impronta ecologica del cemento di CarbiCrete è ridotta ai minimi termini.
Un ultimo esempio di produzione del cemento virtuosa che ci fa ben sperare è quello di Norcem, l’azienda produttrice di cemento più grande in Norvegia. Il gigante ha annunciato la riconversione completa di uno dei suoi maggiori stabilimenti, che verrà trasformato nel primo cementificio a zero emissioni del mondo. L’impianto si trova a Brevik nel Sud della penisola scandinava; già oggi utilizza prevalentemente calore proveniente dall’incenerimento dei rifiuti, ma a partire dai prossimi anni si doterà di tecnologie di Carbon Capture and Storage (CCS) all’avanguardia, per eliminare completamente le sue emissioni entro il 2030.
Insomma, quasi ovunque nel mondo cominciano a fiorire start-up e attività medio-grandi che hanno compreso le enormi opportunità che la transizione energetica può offrire anche alla filiera e alla produzione del cemento. Se vogliamo fermare il cambiamento climatico tuttavia, c’è ancora molto lavoro da fare.