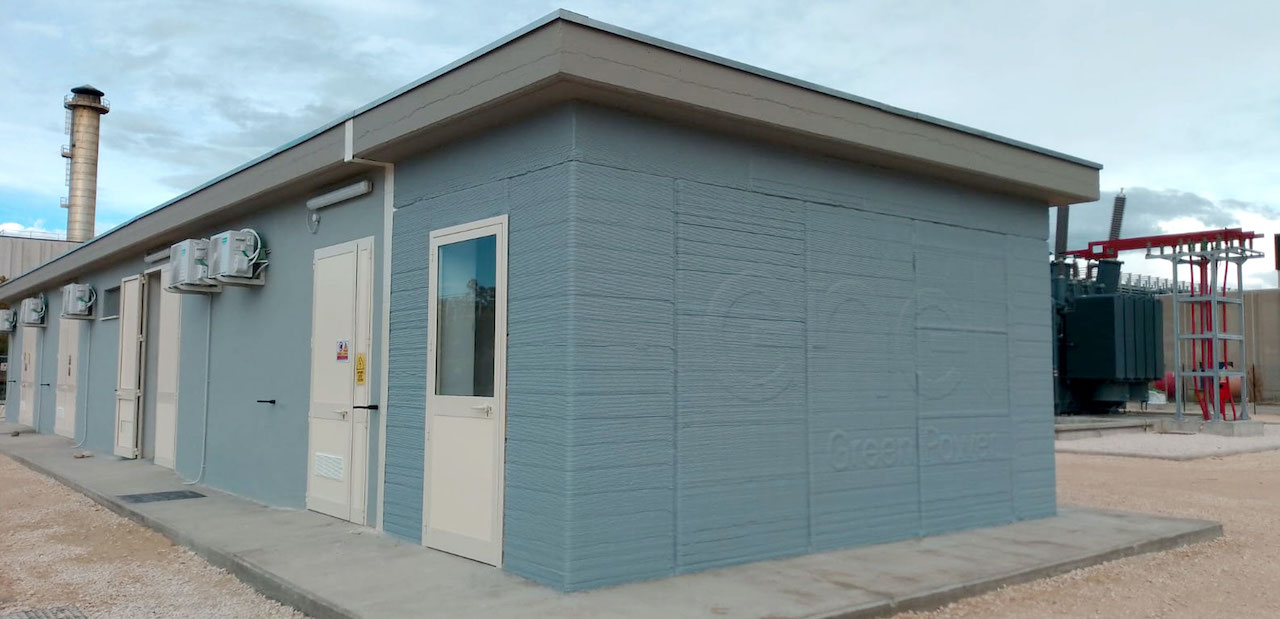
Nel futuro dell’edilizia c’è la stampa 3D con cemento a impatto zero
A Montalto di Castro, nel Lazio, è stato completato il primo edificio antisismico in calcestruzzo stampato in 3D. La struttura sorge nella centrale elettrica “Alessandro Volta” e farà parte di una sottostazione nell’impianto BESS (Battery Energy Storage System). A fornire l’innovativo materiale è la Heidelberg Materials, società leader di settore pronta a produrre il primo cemento a impatto zero in due cementerie in Norvegia ed a Brescia.
La stampa 3D di edifici sarà certamente parte del futuro del mondo delle costruzioni, l’edificio realizzato da Heidelberg Materials in collaborazione con a Enel Green Power e all’Università di Napoli Federico II segna un ulteriore punto a favore di questa tecnologie aprendo la strada verso le soluzioni antisimiche.
Elementi prefabbricati assemblati in cantiere
Adattabilità, velocità di realizzazione, riduzione degli sprechi, sono alcuni degli aspetti positivi della stampa 3D per l’edilizia. A questi si aggiunge la possibilità di produrre forme complesse prefabbricate, assemblabili in un secondo momento in cantiere e che con la tecnica edilizia tradizionale non sarebbe possibile realizzare.
In questo caso, l’edificio antisismico è stato stampato in 3D a Volla (Napoli), grazie alla collaborazione tra l’Università degli Studi di Napoli Federico II con Etesias, spin off della stessa Università. Qui sono state stampate le fondamenta e le pareti poi assemblate a Montalto grazie ad un sistema ad incastri molto simile ai mattoncini Lego.
Il calcestruzzo antisismico “i.tech 3D”
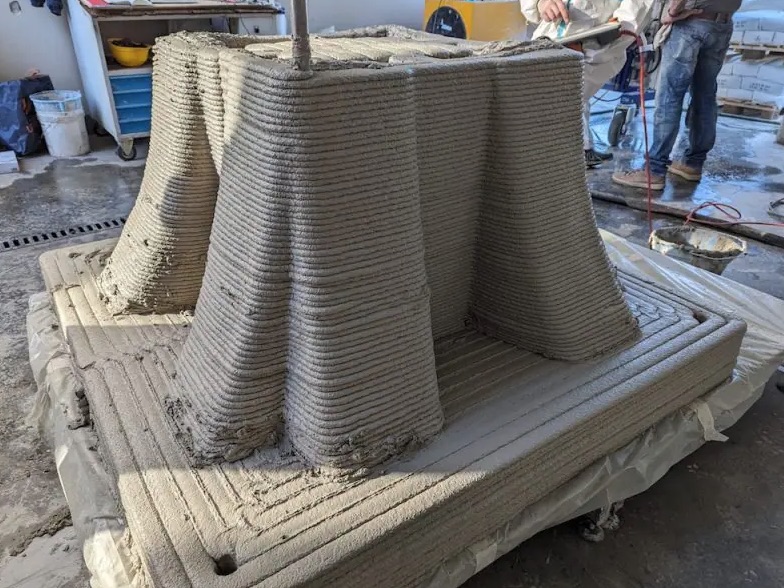
Attraverso la deposizione di un filamento continuo di materiale stampabile in 3D lungo diversi chilometri, un braccio robotico ha costruito i due plinti di fondazione, le pareti e altri componenti utilizzando un modello digitale e un percorso precedentemente progettato utilizzando software specializzato.
Il calcestruzzo che ha permesso di stampare in 3D l’edificio antisismico è l’”i.tech 3D” prodotto dalla Heidelberg Materials.
Nonostante per il momento il calcestruzzo stampabile risulti ancora più costoso rispetto a quello tradizionale, il potenziale è enorme. Il processo costruttivo è più rapido e conveniente con un risparmio di tempo di almeno il 50%. Inoltre si elimina completamente l’uso delle casseformi, riducendo il quantitativo di materiale che finisce in discarica, oltre a ridurre gli sprechi essendo un processo ottimizzato dal software.
Le prestazioni antisismiche della struttura sono state testate nei laboratori dell’Università di Napoli ottenendo così l’autorizzazione da parte del Genio Civile.