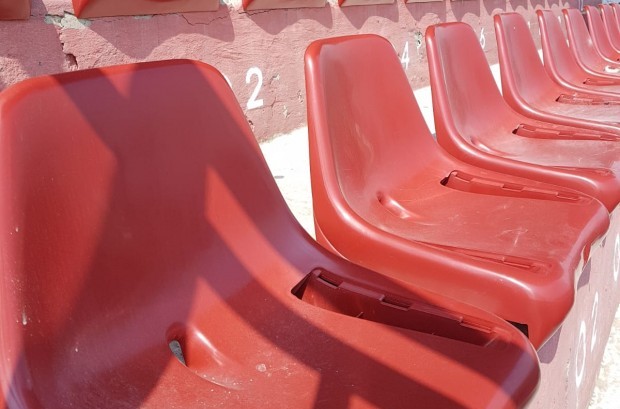
Il riciclo delle plastiche eterogenee ha permesso di ridurre del 30-40% il prelievo di materie prime dall’ambiente
(Rinnovabili.it) – “La città di Pontedera rivendica con soddisfazione ed orgoglio la scelta di aver dotato il proprio stadio comunale con i primi seggiolini al mondo realizzati con le plastiche miste”. Così Matteo Franconi, sindaco del comune pisano, ha presentato ieri il nuovo progetto di riciclo a km zero: nell’impianto sportivo Mannucci sono state installate 3.000 nuove sedute ottenute dai rifiuti, frutto della raccolta raccolta differenziata toscana e del riprocessamento del vicino stabilimento Revet. “Si tratta di una applicazione concreta di quell’economia circolare davvero a km zero – ha affermato Franconi – in cui i rifiuti raccolti, i cittadini che li hanno conferiti, e gli impianti industriali che li hanno ulteriormente selezionati e poi riciclati, sono interamente del nostro territorio: lo stadio Mannucci li utilizza oggi come ri-prodotti”.
>>Leggi anche Riciclo plastica, in Italia l’impianto più efficiente d’Europa<<
L’iniziativa pontederese ha più di un elemento di distinzione. A cominciare dalla materia prima seconda impiegata: si tratta in questo caso di plastiche miste o eterogenee, per loro natura le più difficile da riciclare. Revet, attraverso la sua controllata Revet Recycling, si è affermata in Italia come la prima azienda in grado di dare una seconda vita a questi rifiuti piuttosto che trasformali in combustibile. Dal riciclo delle plastiche miste derivate da imballaggi post-consumo (plasmix), scarti industriali e Raee, oggi nascono tegole, pavimentazioni carrabili, vasi, utensili per la casa, compostiere, articoli per l’edilizia e l’arredamento. E ora anche sedute per impianti sportivi e stadi.
Come spiegato da Livio Giannotti, presidente dell’azienda “L’inaugurazione di oggi corona un lungo lavoro portato avanti da Revet e dal suo ufficio Ricerca e sviluppo che certifica l’elevatissima qualità raggiunta dal nostro granulo. Ora – continua Giannotti – stiamo lavorando alla riduzione dei costi per unità di prodotto, in modo da rendere il prodotto finale competitivo (non solo ambientalmente, ma anche economicamente), con quello realizzato al 100% in materiale vergine, che sfrutta anche le economie di scala finora attuate in tutto il mondo”. Il progetto, condotto in collaborazione con l’azienda bolognese Omsi, consente di ridurre dal 30% al 40% il prelievo di materie prime dall’ambiente.
>>Leggi anche Riciclo plastica, come colmare il divario tra offerta e domanda?<<