Come una costruzione in LEGO, il sistema MOHOHO combina elementi modulari in legno prefabbricati ed uno scheletro strutturale, aprendo l’edificio ad infinite soluzioni costruttive, limitando le risorse e facilitando la manutenzione e sostituzioni dei singoli componenti
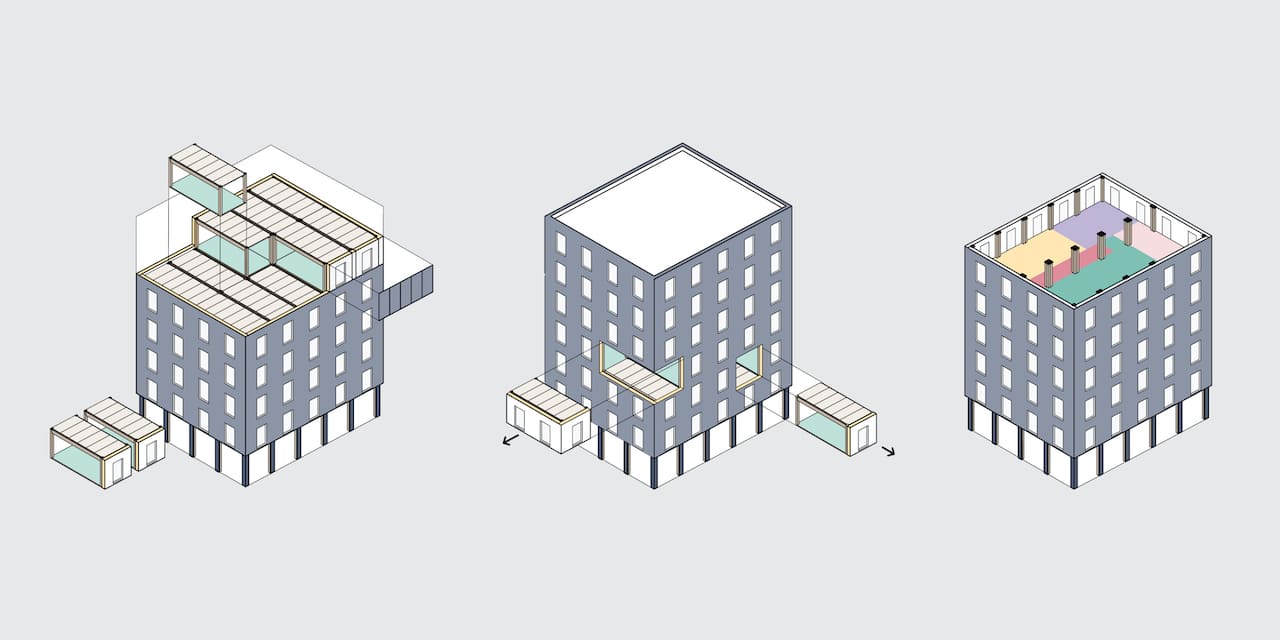
Separare vita operativa e durata di vita di un edificio oggi è ancora molto difficile. La pratica più comune in questi casi è quella di demolire la struttura in disuso e costruirne una nuova che rispecchi le nuove esigenze. Ma in un’ottica di decarbonizzazione che predilige la riqualificazione delle strutture esistenti piuttosto che la nuova costruzione, questa pratica risulta obsoleta. Una soluzione originale ed alternativa potrebbe arrivare dall’architettura modulare in legno.
Un sistema costruttivo che unisce praticità, funzionalità, flessibilità ed impiego di materiali di origine biologica e meno emissivi rispetto ad acciaio e cemento.
E’ nato in quest’ottica il progetto MOHOHO, sviluppato da un team interdisciplinare composto dagli esperti dell’Institute of Architectural Technology e dell’Institute of Timber Engineering and Wood Technology presso la Graz University of Technology (TU Graz), insieme ai partner aziendali Kaufmann Bausysteme e KS Ingenieure.
Le 3 R dell’Architettura modulare
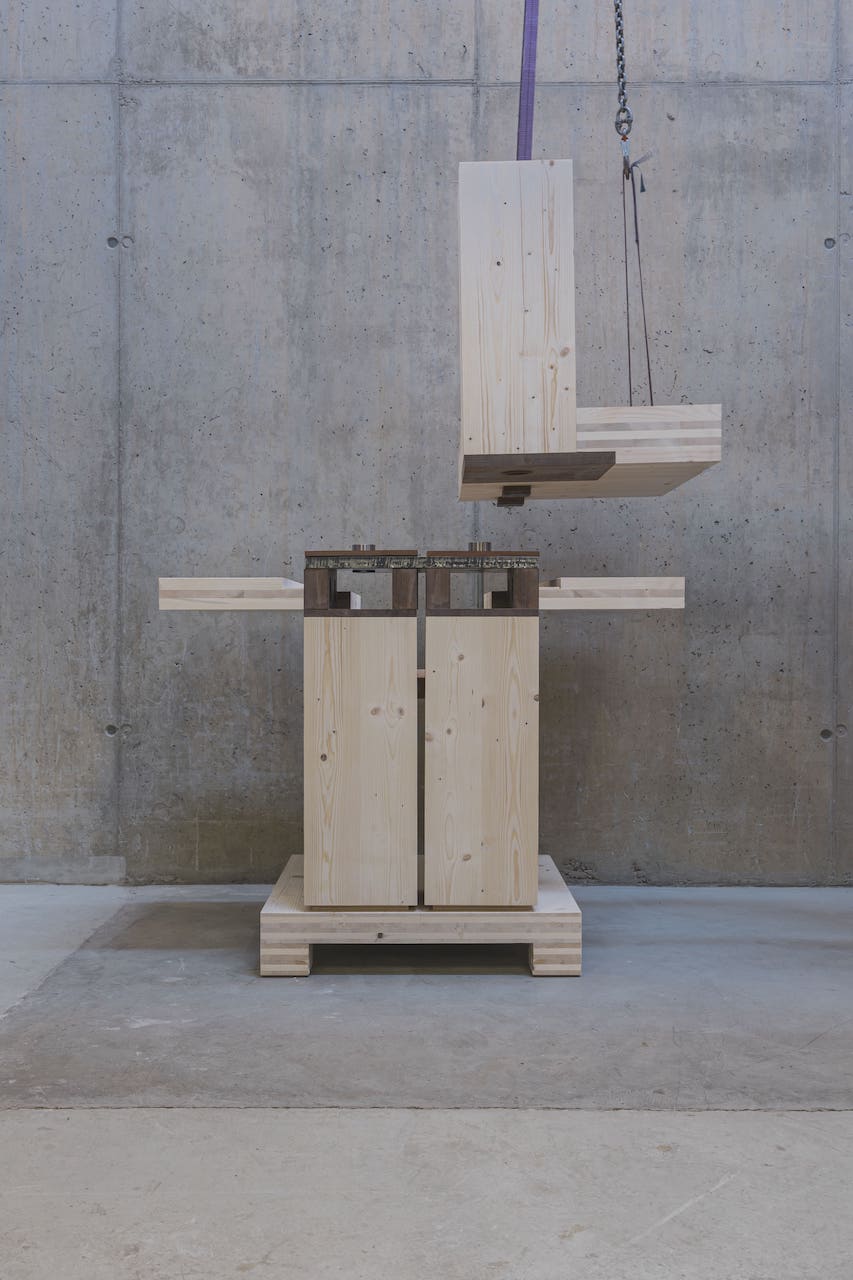
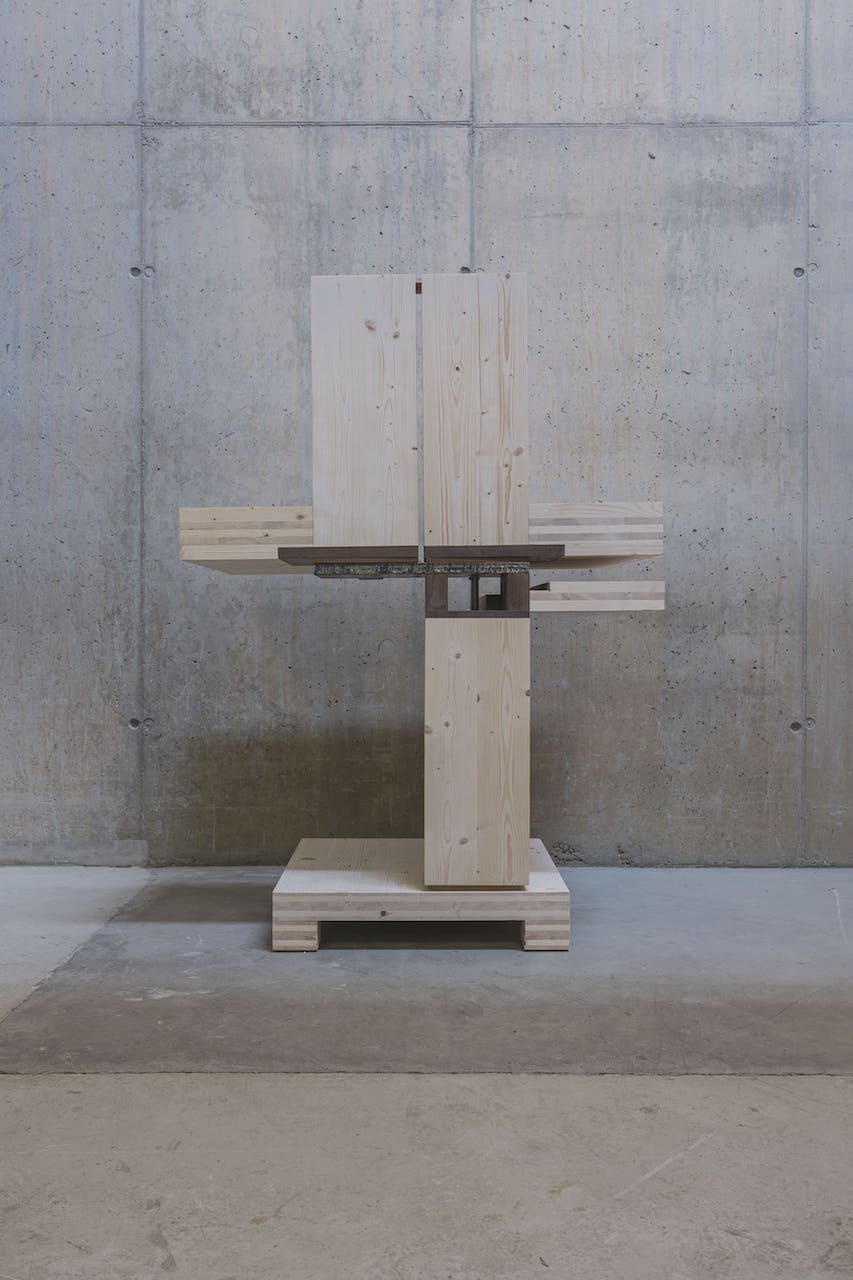
MOHOHO è un sistema costruttivo finalizzato a realizzare un edificio modulare in legno di grandi dimensioni, progettato con lo scopo di estenderne la vita operativa e la durata grazie alla sua adattabilità e flessibilità.
“L’industria edile è responsabile di circa il 60% del consumo globale di risorse e di quasi la metà della produzione globale di rifiuti e delle emissioni globali di gas dannosi per il clima”, sottolinea Christian Keuschnig dell’Istituto di tecnologia architettonica della TU Graz. “Ecco perché le strategie delle 3 R circolari, come la ristrutturazione, la riparazione o il riutilizzo, sono diventate molto importanti per noi nel progetto MOHOHO, per sviluppare un sistema di costruzione che offra un’alternativa a emissioni di CO2 ridotte rispetto ai metodi di costruzione convenzionali nell’edilizia di grattacieli e possa essere utilizzato per scopi diversi il più a lungo possibile”.
Lo scopo è stato raggiunto combinando l’architettura modulare con quella ad intelaiatura:
- la soluzione modulare permette di realizzare elementi in legno 3D completamente prefabbricati, che poi sono impilati accanto o sopra gli uni agli altri;
- mentre l’intelaiatura fornisce una struttura scheletrica di supporto per liberare completamente la planimetria dai vincoli, rendendola adatta a qualsiasi disposizione spaziale.
Gli stessi solai e travi dell’intelaiatura sono realizzati in legno CLT. I vari elementi sono uniti da nodi di incastro preconfigurati, rendendo semplice l’assemblaggio dei pezzi prefabbricati e distribuendo in maniera adeguata i carichi strutturali.
In questo modo si aumenta la robustezza e la sicurezza, facilitando le riparazioni e la manutenzione mirata e puntuale.
Un cuscinetto elastomerico integrato nel nodo garantisce un elevato livello di isolamento acustico tra le unità.
Riparazioni più rapide e veloci
A guadagnarci non è solo il tempo di costruzione e il possibile riutilizzo futuro della struttura, ma anche la praticità della manutenzione.
Per sostituire un modulo o un singolo elemento in legno basta scollegare la rete energetica, quella idrica e l’eventuale sistema di riscaldamento, ed accedere al componente danneggiato. Grazie ad un cilindro di sollevamento inserito di default nel nodo, è possibile separare il componente interessato da quelli adiacenti.
In questo modo di allevia la pressione sui componenti sottostanti e si crea lo spazio necessario per la sostituzione.
Oltre all’accessibilità, i singoli elementi devono poter essere smontati per garantire una costruzione riparabile.
In termini matematici, un’architettura modulare con questo sistema costruttivo può raggiungere un’altezza di ben 24 piani. Tuttavia i tecnici del progetto sottolineano come, oltre i 6 metri d’altezza, sia assolutamente necessario introdurre un nucleo di cemento, fatto che aumenta significativamente il consumo di risorse e le emissioni di CO2.
“La prefabbricazione dei moduli in un capannone di produzione in condizioni controllate consente una maggiore qualità e tracciabilità dei giunti rispetto all’assemblaggio in loco e garantisce tempi di costruzione più brevi nonché una riduzione dell’inquinamento acustico e di rifiuti. La riparabilità e la flessibilità del sistema di costruzione dovrebbero estendere significativamente la vita operativa e la durata di vita dell’edificio. Durante lo smantellamento, i moduli possono essere riutilizzati direttamente o separati per tipo. Stiamo già pianificando un progetto di follow-up in cui vogliamo testare ed esaminare tutte queste cose nella pratica”, ha concluso Christian Keuschnig.
Il sistema è in attesa di brevetto ed ha ricevuto un finanziamento da parte dell’Agenzia austriaca per la promozione della ricerca (FFG).